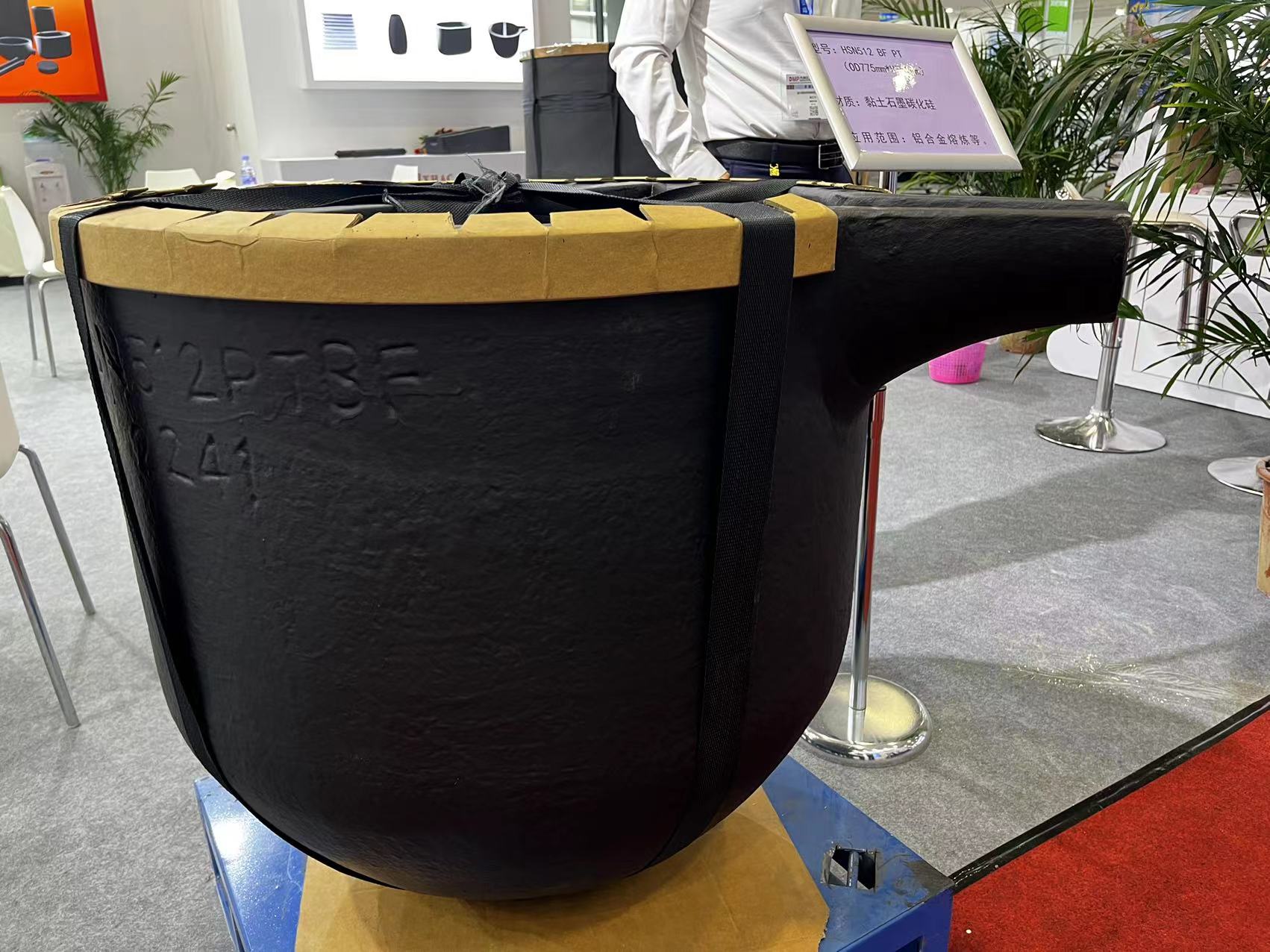
고강도의 준비 방법흑연 실리콘 카바이드 도가니금속 제련의 경우 다음 단계가 포함됩니다. 1) 원료 준비; 2) 1 차 혼합; 3) 재료 건조; 4) 분쇄 및 스크리닝; 5) 2 차 재료 준비; 6) 2 차 혼합; 7) 프레스 및 성형; 8) 절단 및 트리밍; 9) 건조; 10) 유약; 11) 1 차 발사; 12) 함침; 13) 2 차 발사; 14) 코팅; 15) 완제품. 이 새로운 공식 및 생산 공정을 사용하여 생산 된 도가니는 강한 고온 저항성과 부식 저항을 가지고 있습니다. 도가니의 평균 수명은 7-8 개월에 이르며, 균일하고 결함이없는 내부 구조, 고강도, 얇은 벽 및 우수한 열전도율로 이루어집니다. 또한, 다중 건조 및 발사 공정과 함께 표면의 유약 층 및 코팅은 높은 수준의 유리화로 제품의 부식 저항을 크게 향상시키고 에너지 소비를 약 30%줄입니다.
이 방법은 비철 금속 주조의 분야, 특히 금속 제련을위한 고강도 흑연 실리콘 카바이드 도가니의 제조 방법을 포함한다.
[배경 기술] 특수 흑연 실리콘 카바이드 도가리는 주로 비철 금속 주조 및 위조 공정, 귀금속의 회복 및 정제, 고온 및 부식성 제품의 생산에 주로 사용됩니다.
기존의 특수 흑연 실리콘 카바이드 도가니 형성 및 생산 공정은 평균 수명이 55 일인 제품을 생산하여 너무 짧습니다. 사용 및 생산 비용은 계속 증가하고 있으며 생성 된 폐기물의 양도 높습니다. 따라서, 새로운 유형의 특수 흑연 실리콘 카바이드 Crucible과 그 생산 공정을 연구하는 것은 다양한 산업 화학 분야에서 중요한 응용을 가지고 있기 때문에 해결해야 할 긴급한 문제입니다.
상기 문제를 해결하기 위해, 금속 제련을위한 고강도 흑연 실리콘 카바이드 도가니를 제조하는 방법이 제공된다. 이 방법에 따라 제조 된 제품은 고온과 부식에 강하고 서비스 수명이 길며 생산 중에 에너지 절약, 배출 감소, 환경 보호 및 높은 재활용 비율을 달성하여 자원의 순환 및 활용을 극대화합니다.
금속 제련을위한 고 강성 흑연 실리콘 카바이드 도가약의 제조 방법에는 다음 단계가 포함됩니다.
- 원자재 준비 : 실리콘 카바이드, 흑연, 점토 및 금속 실리콘은 크레인에 의해 각각의 성분 호프퍼에 배치되며, PLC 프로그램은 필요한 비율에 따라 각 재료의 방전 및 무게를 자동으로 제어합니다. 공압 밸브는 방전을 제어하고 각 성분 호퍼의 바닥에 최소 2 개의 계량 센서가 설정됩니다. 무게를 측정 한 후, 재료는 자동 이동 가능한 카트에 의해 혼합 기계에 배치됩니다. 탄화물의 초기 첨가는 총 금액의 50%입니다.
- 2 차 혼합 : 원료가 혼합 기계에서 혼합 된 후에는 버퍼 호퍼로 배출되며, 버퍼 호퍼의 재료는 2 차 믹싱을 위해 버킷 엘리베이터에 의해 혼합 호퍼로 들어 올립니다. 철 제거 장치는 버킷 엘리베이터의 배출 포트에 설정되며, 물 첨가 장치가 믹싱 호퍼 위에 놓여 교반하는 동안 물을 첨가합니다. 물 첨가 속도는 10L/분입니다.
- 재료 건조 : 혼합 후 습식 물질은 120-150 ° C의 온도에서 건조 장비에서 건조되어 수분을 제거합니다. 완전 건조 후, 재료는 자연 냉각을 위해 꺼집니다.
- 분쇄 및 스크리닝 : 건조 된 덩어리 재료는 사전 크러싱을위한 분쇄 및 스크리닝 장비로 들어간 다음 더 큰 분쇄를 위해 카운터 택 크러셔로 들어가 동시에 60 메시 스크리닝 장비를 통과합니다. 0.25mm보다 큰 입자는 추가 사전 크러싱, 분쇄 및 스크리닝을 위해 재활용을 위해 반환되는 반면, 0.25mm보다 작은 입자는 호퍼로 전송됩니다.
- 2 차 재료 준비 : 방전 호퍼의 재료는 2 차 준비를 위해 배치 기계로 다시 운반됩니다. 실리콘 카바이드의 나머지 50%가 2 차 준비 동안 첨가된다. 2 차 준비 후 재료는 혼합을 위해 혼합 기계로 전송됩니다.
- 2 차 혼합 : 보조 혼합 공정 동안, 점도가있는 특수 용액이 특정 중력을 갖는 특수 용액 첨가 장치를 통해 혼합 호퍼에 첨가된다. 특수 용액은 계량 버킷으로 무게를 측정하고 믹싱 호퍼에 첨가합니다.
- 프레스 및 성형 : 2 차 믹싱 후 재료는 등방성 프레스 머신 호퍼로 전송됩니다. 곰팡이의 로딩, 압축, 진공 청소기 및 청소 후, 재료는 등방성 프레스 기계에 누릅니다.
- 절단 및 트리밍 : 여기에는 높이를 자르고 도가니 버를 다듬는 것이 포함됩니다. 절단은 절단 기계에 의해 도가니를 필요한 높이로 자르고 절단 후 버를 잘라냅니다.
- 건조 : (8) 단계에서 절단 및 손질 후 도가니는 건조 온도가 120-150 ° C 인 건조 오븐으로 보내집니다. 건조 후 1-2 시간 동안 따뜻하게 유지됩니다. 건조 오븐에는 공기 덕트 조정 시스템이 장착되어 있으며, 이는 여러 조절 식 알루미늄 플레이트로 구성됩니다. 이 조절 가능한 알루미늄 플레이트는 건조 오븐의 두 안쪽면에 배열되며, 두 개의 알루미늄 플레이트마다 공기 덕트가 있습니다. 두 개의 알루미늄 플레이트마다 간격이 공기 덕트를 조절하도록 조정됩니다.
- 유약 : 유약은 유약 물질을 벤토나이트, 내화 점토, 유리 분말, 장석 분말 및 나트륨 카르복시 메틸 셀룰로스를 포함한 물과 혼합하여 만들어집니다. 유약은 유약 중에 브러시로 수동으로 적용됩니다.
- 1 차 발사 : 적용된 유약이있는 Crucible은 28-30 시간 동안 1km에서 한 번 발사됩니다. 발사 효율을 향상시키기 위해 밀봉 효과 및 공기 막힘이있는 미로 가마 침대가 가마의 바닥에 설정됩니다. 가마 침대에는 밀봉면의 바닥 층이 있으며 밀봉면 위에는 단열 벽돌 층이있어 미로 가마 침대를 형성합니다.
- 함침 : 발사 된 도가니는 진공 및 압력 함침을 위해 함침 탱크에 배치됩니다. 함침 솔루션은 밀봉 된 파이프 라인을 통해 함침 탱크로 운반되며 함침 시간은 45-60 분입니다.
- 2 차 발사 : 함침 된 도가니는 2 시간 동안 2 차 발사를 위해 가마에 배치됩니다.
- 코팅 : 2 차 발사 후 도가니는 표면에 수성 아크릴 수지 페인트로 코팅됩니다.
- 완제품 : 코팅이 완료된 후 표면이 건조되고 건조 후 도가니가 포장되어 저장됩니다.
후 시간 : 3 월 20 일 -20124 년